Throwback Thursday: The Spanish 2 Bottom Bracket
10 years ago
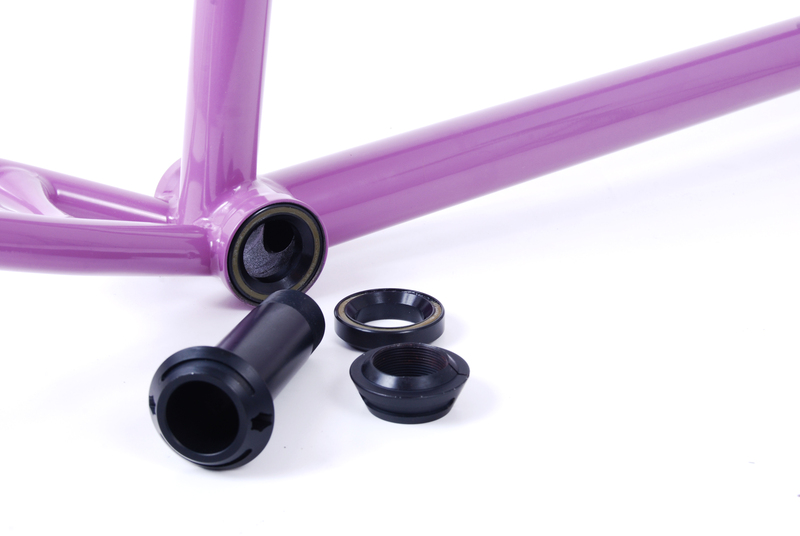
As with every Flybikes product, we try to produce a product that is high quality while doing our best to simplify the design and give it a clean aesthetic look that represents the quality. Over the years, we have developed and produced many products, always changing and evolving to make things better than before. With that development comes a lot of trial, error and ideas that simply do not make it past testing because it does not meet our quality standards.
Since today is Thursday, we figured it would be fun to do a little “Throwback Thursday” and look back at one of those concepts that never made it beyond the testing phase back in 2008; the Spanish 2 bottom bracket.
The concept of the Spanish 2 was to create a bottom bracket that could be installed similar to an integrated headset, without needing a hammer to press the bearings in place. As you can see by the photo, we developed tapered bearings similar to integrated headset bearings that were pressed into the bottom bracket shell with a two-piece spindle spacer that had tapered covers to press the bearings in place with one side that is threaded for tensioning.
During testing, we developed two versions; one with regular tapered covers and one with taped covers that had grub screws, to ensure the bottom bracket would remain tight. Sadly, the issue wasn’t in the spindle spacer and covers, but the bearings. The tapered bearings could not handle the stress that the cranks put on them and would blow out.
Although this concept never made it to shops, the idea is something we can look back on and know that we at least tried and learned from. It’s better to try and fail than to never know.
Since today is Thursday, we figured it would be fun to do a little “Throwback Thursday” and look back at one of those concepts that never made it beyond the testing phase back in 2008; the Spanish 2 bottom bracket.
The concept of the Spanish 2 was to create a bottom bracket that could be installed similar to an integrated headset, without needing a hammer to press the bearings in place. As you can see by the photo, we developed tapered bearings similar to integrated headset bearings that were pressed into the bottom bracket shell with a two-piece spindle spacer that had tapered covers to press the bearings in place with one side that is threaded for tensioning.
During testing, we developed two versions; one with regular tapered covers and one with taped covers that had grub screws, to ensure the bottom bracket would remain tight. Sadly, the issue wasn’t in the spindle spacer and covers, but the bearings. The tapered bearings could not handle the stress that the cranks put on them and would blow out.
Although this concept never made it to shops, the idea is something we can look back on and know that we at least tried and learned from. It’s better to try and fail than to never know.